PRODUCTION
PRODUCTION
The SMT (Surface Mounted Technology) department is responsible for one of the most important stages of the production process: PCB production. The workshop can deliver up to 6000 pcs/day and strictly follows IPC-A-610 inspection standard, which sets very high requirements for the high reliability printed circuit assemblies.
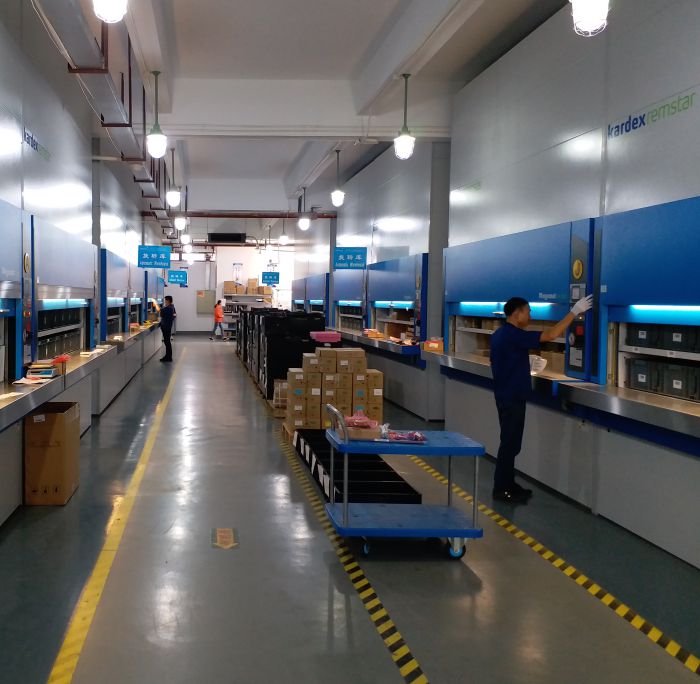
SMT Automatic Storage System
This Kardex Automatic Storage System (Sweden) is made of modules with 21 layers each, 7 boxes/layer, and guarantees high capacity, easy component retrieval and safety.
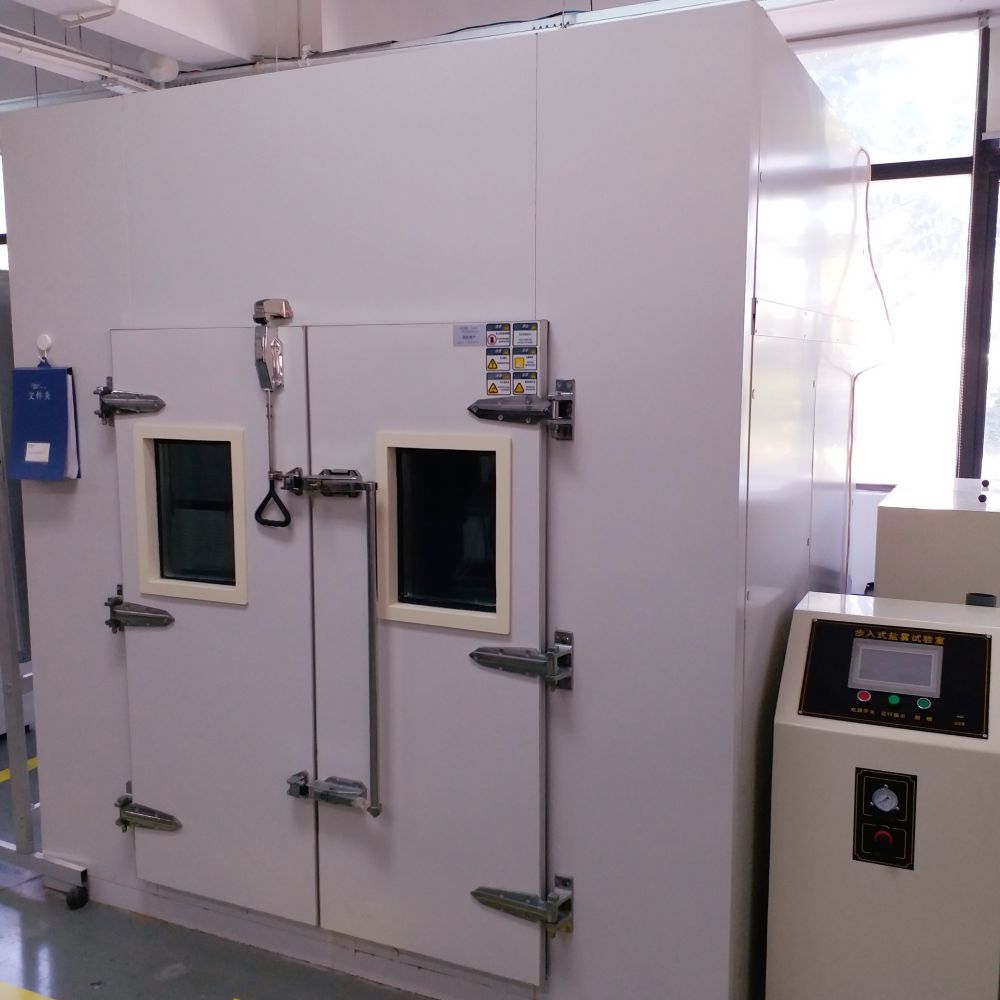
SMT
WORKSHOP
SMT workshop (PCB boards printing and assembly) is the first stage of production and it’s made of world class equipment for Jet Printing (MYCRONIC – former MYDATA), components Pick & Place (JUKI) and Wave & Selective Reflow Soldering (ERSA) machines.
A series of tests are made both automatically (AOI equipment) and manually before the PCB boards are ready for the next production stage.
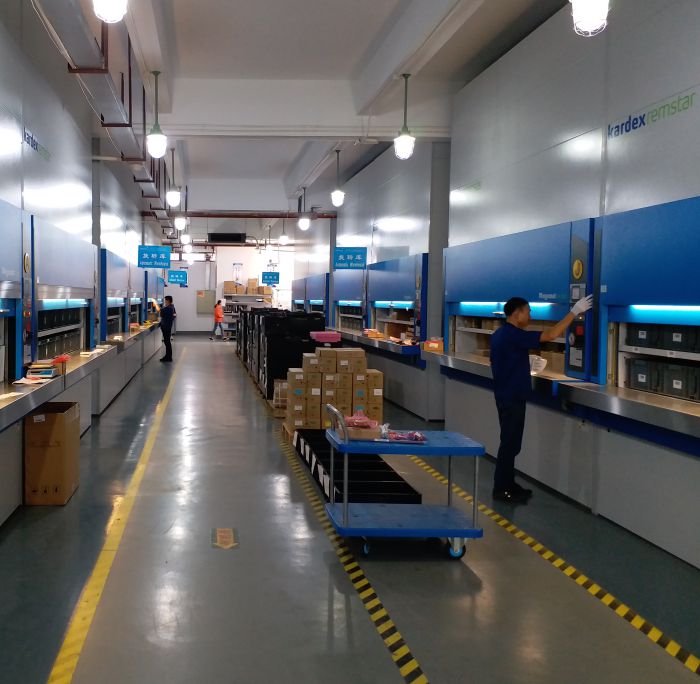
SMT Automatic Storage System
This Kardex Automatic Storage System (Sweden) is made of modules with 21 layers each, 7 boxes/layer, and guarantees high capacity, easy component retrieval and safety.
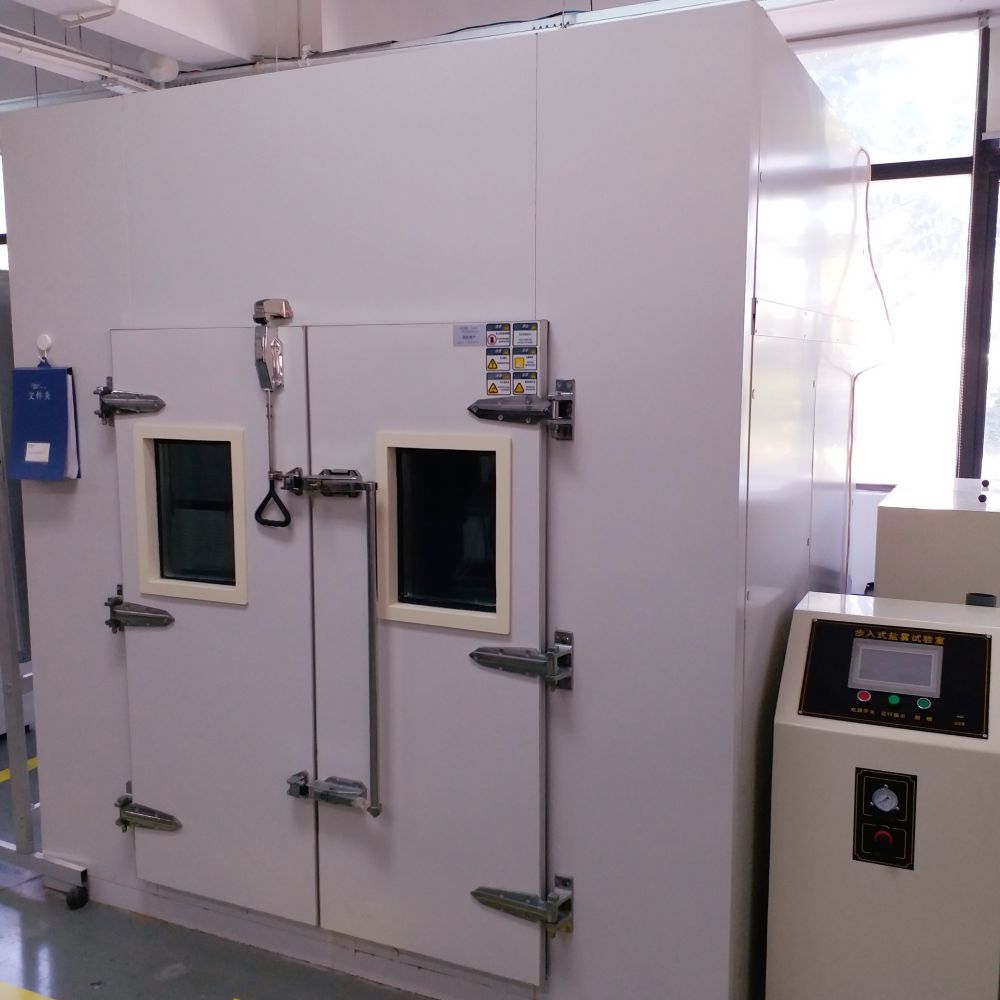
SMT WORKSHOP
SMT workshop (PCB boards printing and assembly) is the first stage of production and it’s made of world class equipment for Jet Printing (MYCRONIC – former MYDATA), components Pick & Place (JUKI) and Wave & Selective Reflow Soldering (ERSA) machines.
A series of tests are made both automatically (AOI equipment) and manually before the PCB boards are ready for the next production stage.
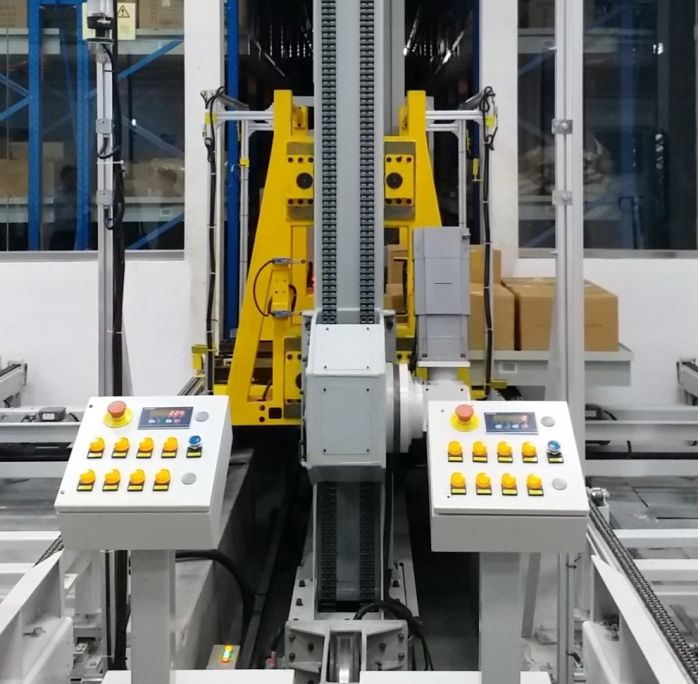
Factory ASRS
This Automatic Storage and Retrieval System allows to maximize space utilization, efficiency and reduces greatly labour costs.
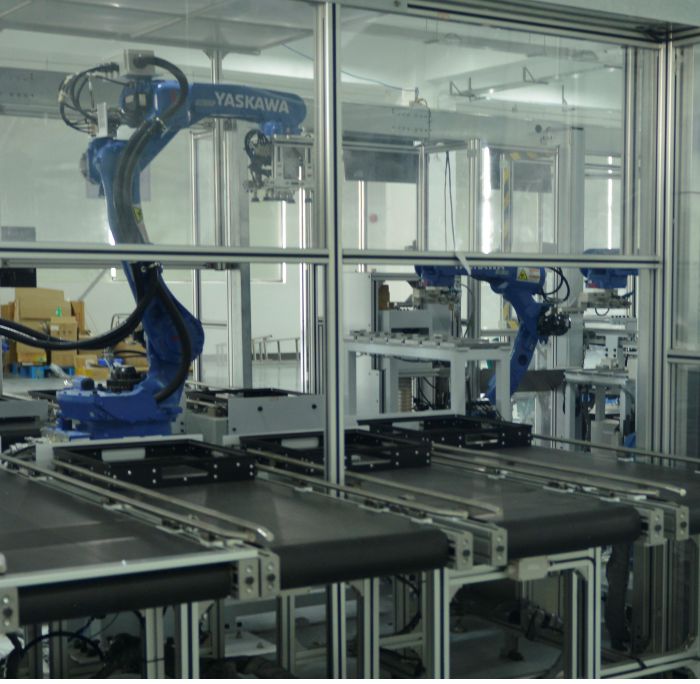
AUTOMATED POWER PCB ASSEMBLY LINE
This high-tech assembly line is made of 8 robots and it has an output of up to 50 units/hr, making this stage of production human error-free, efficient and safe.
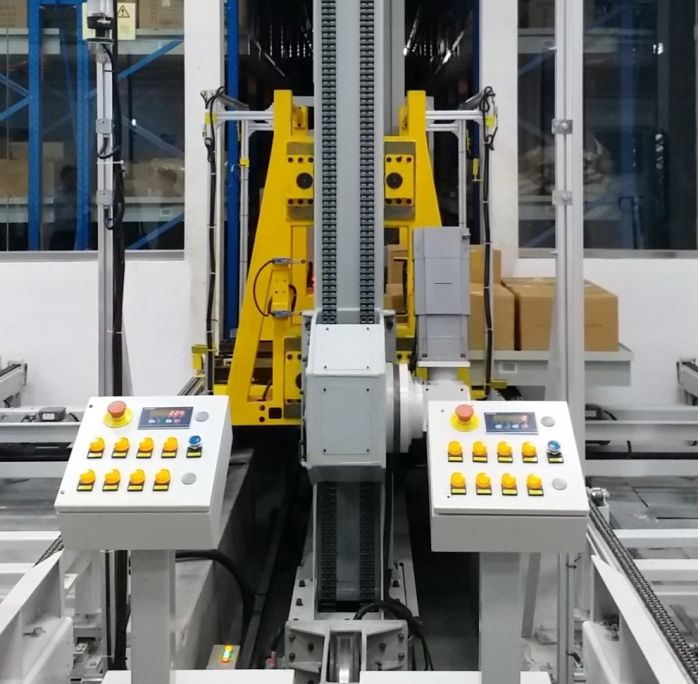
Factory
ASRS
This Automatic Storage and Retrieval System allows to maximize space utilization, efficiency and reduces greatly labour costs.
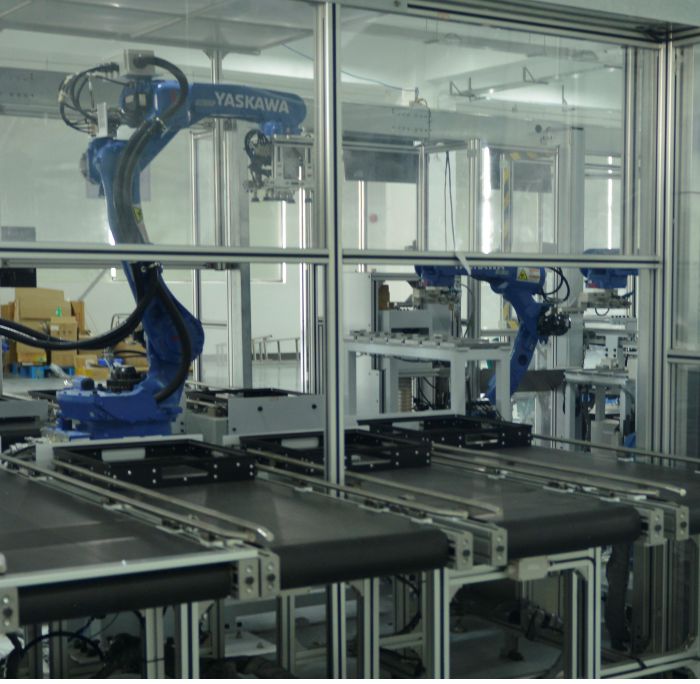
AUTOMATED POWER PCB ASSEMBLY LINE
This high-tech assembly line is made of 8 robots and it has an output of up to 50 units/hr, making this stage of production human error-free, efficient and safe.
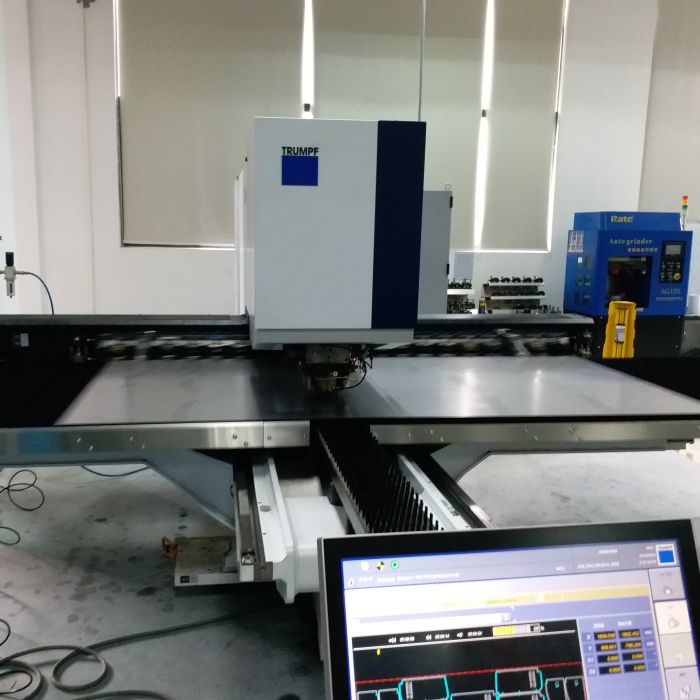
METAL CASE WORKSHOP
Product metal casing is made by an automatic metal sheet feeding system, for being then processed by laser cutting and punching machines. Before being sent to the final product assembly line, casings are painted by an electrostatic powder coating system which meet the latest standards for environmental protection.
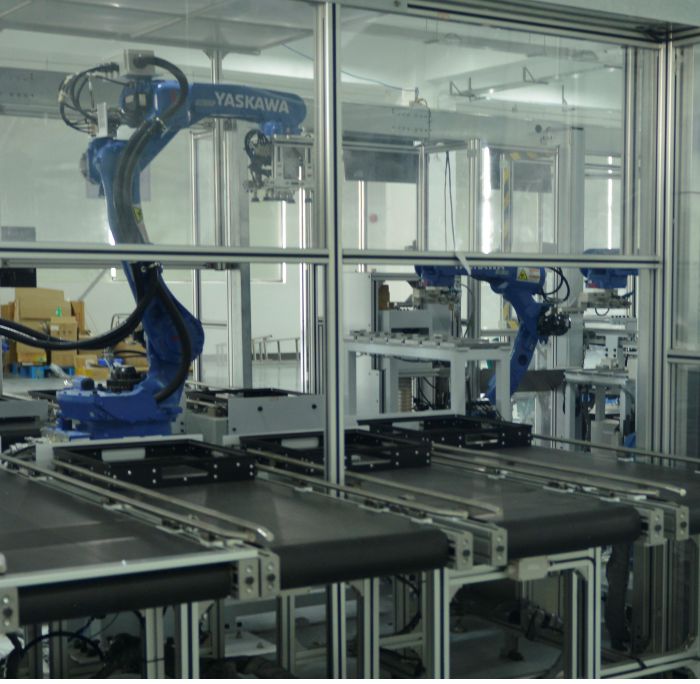
ASSEMBLY
LINES
Each assembly line is in charge either for small inverter machine or for bigger equipment. The factory employs around 300 workers.
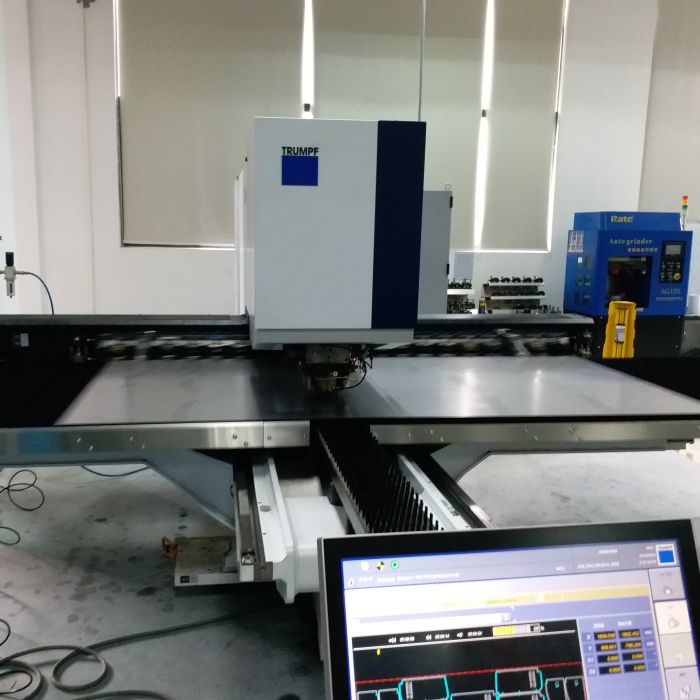
METAL CASE WORKSHOP
Product metal casing is made by an automatic metal sheet feeding system, for being then processed by laser cutting and punching machines. Before being sent to the final product assembly line, casings are painted by an electrostatic powder coating system which meet the latest standards for environmental protection.
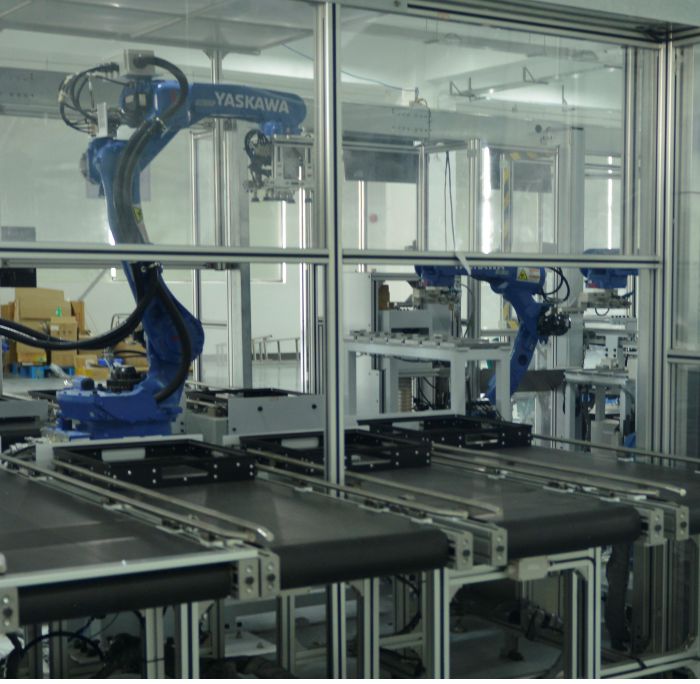
ASSEMBLY LINES
Each assembly line is in charge either for small inverter machine or for bigger equipment. The factory employs around 300 workers.
OUR QUALITY ASSURANCE IS MADE OF:
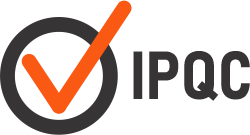
INCOMING PRODUCTS
QUALITY CONTROL
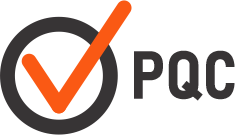
PROCESS
QUALITY CONTROL
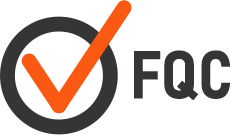
FINISHED PRODUCTS
QUALITY CONTROL
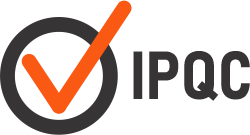
INCOMING PRODUCTS
QUALITY CONTROL
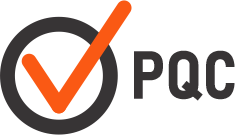
PROCESS
QUALITY CONTROL
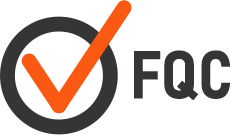
FINISHED PRODUCTS
QUALITY CONTROL
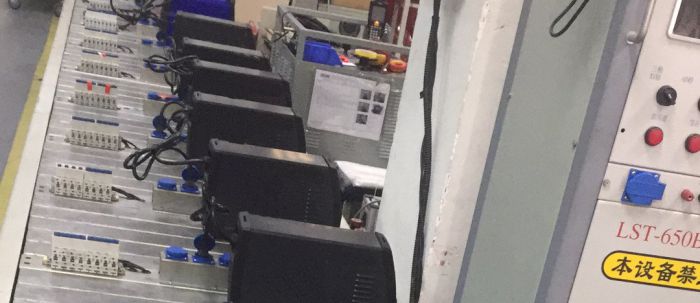
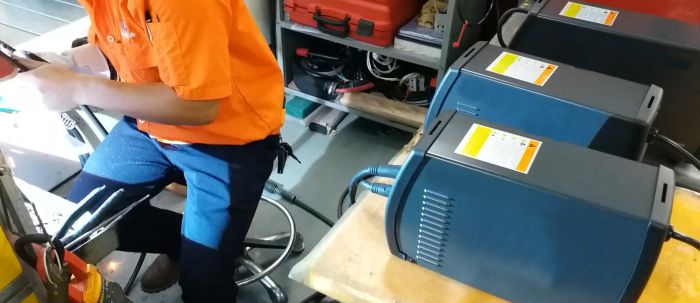